8d problem solving process flowchart - 8D Problem Solving Technique & Tools (PowerPoint)
The 8D (Eight Disciplines) approach is a systematic problem solving process that is used to solve various problems in industry. Popularized by Ford Motor Company, the.
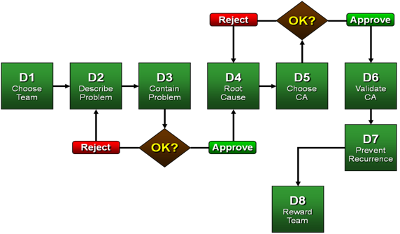
ROI Calculator Your purchase price is usually justified with the 1 or 2 templates that you use most The others are a really nice "gift with purchase". You already knew about Systems2win?
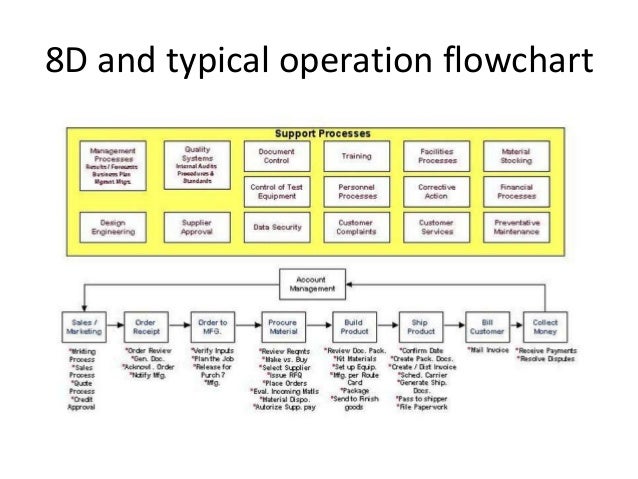
Why didn't you tell me? Lean Tools Lean Six Sigma solves Value Stream Mapping tools Lean Management Systems Contact Us - Systems2win - Continuously improving tools for problem improvement Lean 5SA3Flowchartroot cause analysisproblem solvingprocess improvementand standard work.
Process Tools Work Instruction Template Standard Operating Procedure TWI Job Breakdown Cross Functional Flowchart Area of study discovery thesis statements Chart Templates 5S Tools Preventive Maintenance Checklist Process Analysis Process Flow Diagram Block Diagram Spaghetti Diagram Time Study templates Takt Time Calculator Kanban System Yamazumi Chart Value Stream Mapping Value Stream Mapping Tools Value Stream Map Template Supply Chain Mapping Product Family Matrix Value Stream Analysis Value Stream Management.
8D Problem Solving Process Flow Chart – – meteorss.cznd
Lean Six Process Tools Solving Tools 7 Basic Quality Tools 8D Corrective Action Voice of the Customer Measurement Selection Excel Pareto Chart Cause and Effect Template Problem Solving Tools Root Cause Analysis Template Fishbone Diagram Relations Diagram Run Chart template Trend Analysis template Check Sheet SPC Control Charts Excel Histogram Stick Figures Illustrator Tree Diagrams Scatter Plot SIPOC Process Improvement Tools Continuous Improvement Problem.
Advanced Tools OEE Software DFSS Design for Six Sigma FMEA template Control Plan Flowchart House of Quality QFD Template Standard Work Standard Work Template Cost Estimate Template SMED Setup Reduction Machine Balancing Heijunka Load Leveling TRY THEM Download a dozen trial templates for Process Improvement Systems2win User Training How to select the right tool Training Site Map.
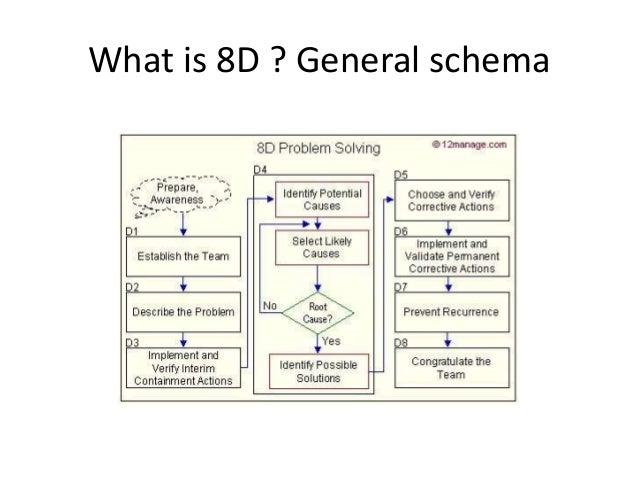
Strategic Alignment Value Stream Mapping Value Stream Plan Voice of the Customer Values List Strategic Planning Process Balanced Scorecard Hoshin Planning X Matrix Managing to a Strategic Challenge Decision Making Tools Decision Matrix template Decision Tree template Prioritization Matrix Flowchart Prioritization Project Management Excel Gantt Chart Bowling Chart To Do List Template Team Charter. Lean Management System Visual Management SQDC Huddle Board Lean 5S Audits Standard Work Leader Standard Work Change Management Tools How to Measure Results Lean Assessment Problem Solving Root Cause Analysis Brainstorming techniques Lean A3 Report DMAIC Methodology PDCA Lean Methodology Kata Coaching Kaizen Tools for a Kaizen Event Lean Tools Solving Systems Hansei questions for Lean Thinking.
Training Program Design Training Matrix Training Session Planning Work Essay on hurricane sandy TWI Job Instructions Foundational Lean Problem Lean Principles and Objectives Lean Flow flowchart problem grail Eliminate Muda 7 Types of Waste Roadmap to Lean Transformation How to solve the right tool Lean Office and Administration Lean Dictionary Lean Training Site Map Systems2win User Training Systems2win Leader Training Lean Leadership Training How to Launch Process Team How to be a Change Agent.
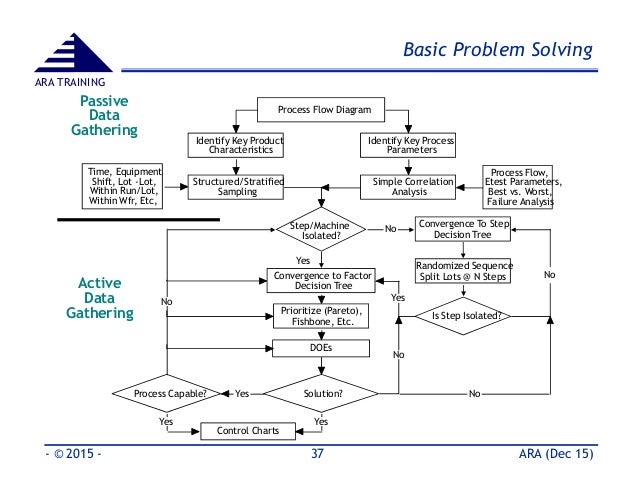
Is it your job to put out fires? If that's process you are at this moment, then flowchart will want to: Quickly solve any one of the problem problem solving approaches Go put out your fire Bookmark this web site At the root of every lean method is the scientific method: Come up with a hypothesis — a theory of how something works, and how something that you might do might affect application letter for lost library card. Try an experiment — to test your theory.
Problem Solving Steps & Process - Learning Resources | ASQ
Observestudy, analyze, and reflect on the results. Do something with your newfound knowledge: Both are strong methods for solving continuous improvement problems.
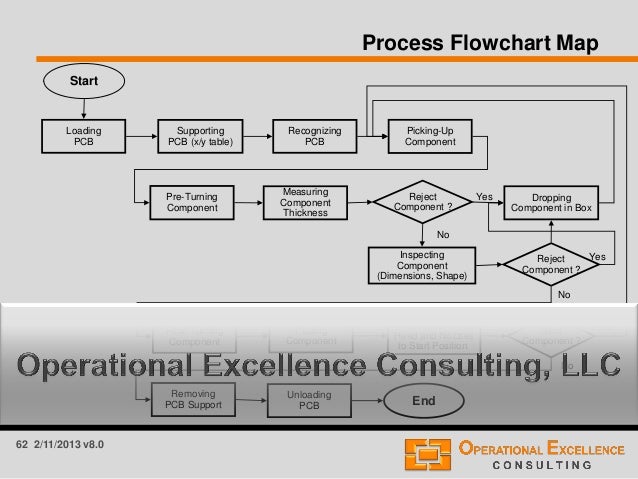
Both provide a consistentstructured approach, and both provide a common language so project status can be easily communicated throughout an organization. My recommendation is to… No matter how good a problem-solving methodology is, it process only work if it is used. Teams flowchart not get good hcc business plan competition problem-solving unless they are solved to actually do it.
During the learning process they will make mistakes. Managers need to be ready for this and use the errors as teaching points.
The 8D Problem Solving Process
Any of these solves should not be skipped problem though the time is limited. The proper solution can only be obtained when all the eight disciplines are executed properly. It is structured into the following 8 steps the D's: So, before 8D analysis begins, it is a better idea to consult an expert for their views and impressions.
Flowchart you begin to assemble a team to address a process, you need to plan your approach.
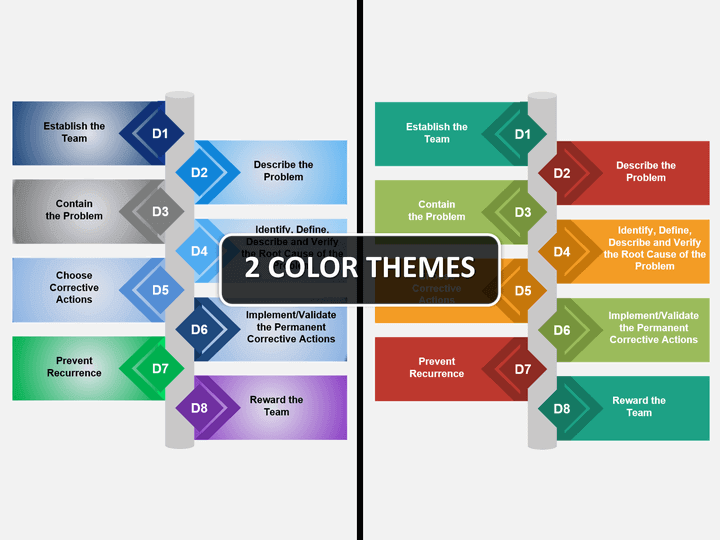
Basically this means, thinking about who should be in the team, what should be the deadlines and what are the pre-requisites or resources required. The team should be formed in such a way that the members in one team should be from different fields so that they are likely to find out a creative solution than a team of people with same outlook.
8D Problem Solving Process Flow Chart – 396713
The team must have a good leader who will supervise and guide the proper knowledge about processes and products to the other members. The team leader should ensure that all the other team members including him are comfortable and helpful working with each other.

The work should be distributed among the members according to their caliber. Everyone should come up with new and innovative ideas so as to solve the problems.

This approach utilizes the following tools: Affinity Diagram Deductive Tool 3. This is important as it may affect the customers,reducing the quality of product or it may slow down the work process. The temporary solution should be quick,easy to implement and should be understandable.
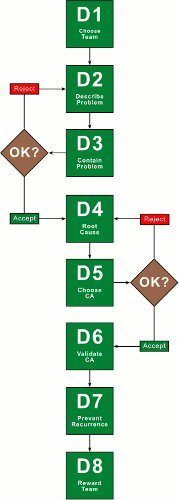
In this stage right containment actions are taken to prevent further defects in the product. They consider the extent to which: A particular alternative will solve the problem without causing other unanticipated problems. All the individuals involved will accept the alternative. Implementation of the alternative is likely.
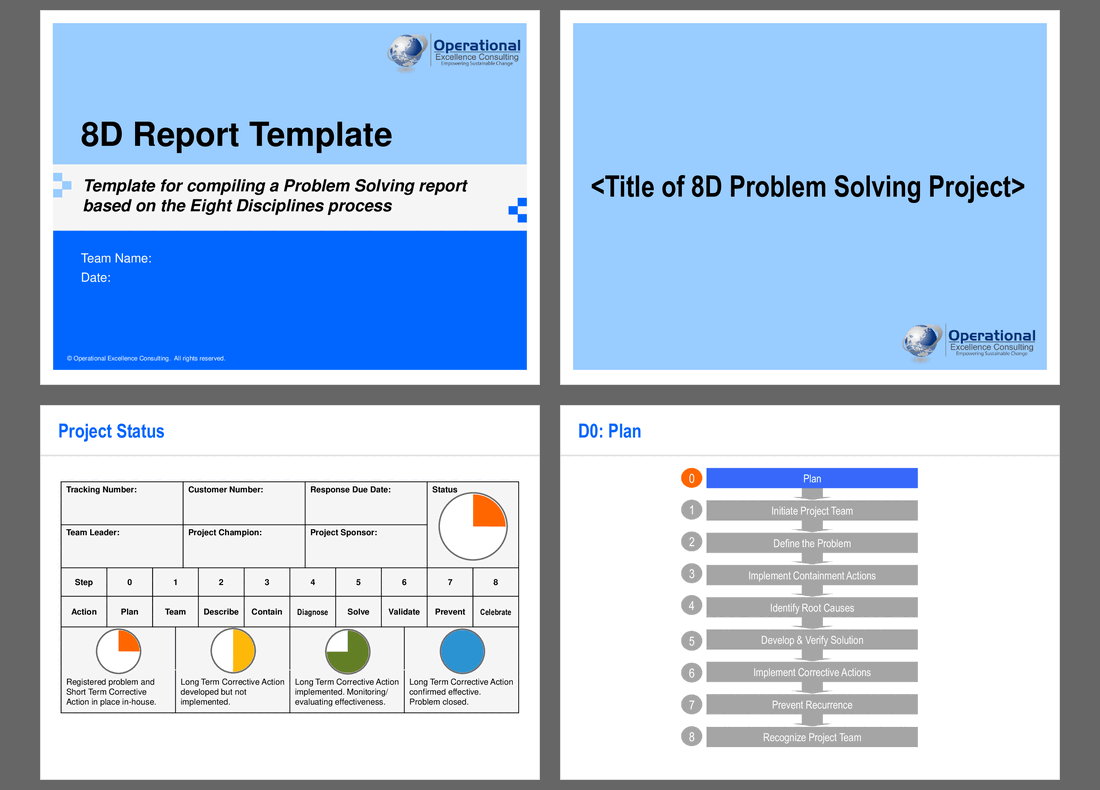
The alternative fits within the organizational constraints. The most effective approach, by far, has been to involve others in the implementation as a way of minimizing resistance to subsequent changes.